This article is from Nexen Group Inc. a partner of DIRECTPNEUMATICS.COM.
Branded as Industry 4.0, the fourth industrial revolution is still in its infancy. Manufacturers and suppliers are grappling with the concept of Industry 4.0, and they are individually determining what 4.0 means to them.
Broadly defined, Industry 4.0 is the integration of automation with data exchange to optimize performance. It relies heavily on both cyber-physical systems, which are digital copies of the physical work environment, and cognitive computing, in which computers make decisions and instruct machines to perform tasks.
Industry 4.0 allows for greater customization of products. A liquid manufacturer, for example, could use 4.0 systems to tailor the formula for each customer. A digital chip on each bottle instructs devices at each stop in the production process to pour the correct amount of each ingredient for the specific formula for that bottle. At the end of the process, each bottle is labeled according to its formula.
Similarly, 4.0 technology can be used to optimize the load distribution of shipping containers as they are loaded on cargo freighters. Cranes equipped with sensors that measure the weight of each shipping container as it is lifted can work in concert with digital modeling of a ship to identify the best location for each container to minimize fuel consumption during the voyage.
Introduced as a concept in 2011, Industry 4.0 has been reshaping industry, much as did the previous industrial revolutions. The first of those revolutions was driven by the introduction of steam and water power in the 1700s. In the early 1900s, the assembly line and electricity led to mass production. And in the 1970s, computers and automation changed assembly lines.
The ultimate goal of Industry 4.0 is creating smart factories. With its convergence of physical and cyber systems, 4.0 has implications for forecasting, development cycles, asset utilization, automation, productivity, supply-chain management and after-sales services.
As manufacturers adopt 4.0, companies that build the equipment used in factories are retooling their machines and devices to generate data to improve decision- making by both computers and human operators.
4.0 Compatible Zero-Backlash Brakes
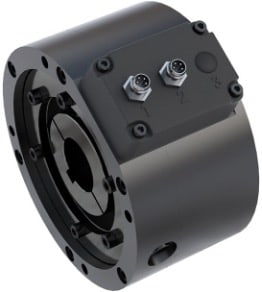
In February 2018, Nexen unveiled 4.0-compatible versions of its ZSE brakes. Designed to stop and hold loads as they reach new stations in a production process, ZSE brakes are typically used for through-shaft setups, positioning indexers, conveyor systems and trunnion tables.
One such equipment manufacturer is Nexen Group Inc., which specializes in precision motion-control components such as zero-backlash, spring-engaged (ZSE) brakes.
Based in Vadnais Heights, MN, Nexen has chosen to focus its contributions to Industry 4.0 in nine of 21 domains, including remote monitoring and control, human-machine collaboration, real-time yield optimization, smart energy consumption and predictive monitoring.
In February 2018, Nexen unveiled 4.0-compatible versions of its ZSE brakes. Designed to stop and hold loads as they reach new stations in a production process, ZSE brakes are typically used for through-shaft setups, positioning indexers, conveyor systems and trunnion tables. The smart versions of Nexen’s ZSE brakes are equipped with internal temperature sensors and disengagement-verification sensors that provide feedback that engineers and technicians can access from computers in a control room and from hand-held tablets used on the manufacturing floor.
If the temperature sensor detects that the heat level is outside that of normal operation, that could indicate that the ZSE smart brake may have been installed improperly, it may require maintenance, or it may be reaching its end of life.
The temperature sensor allows maintenance personnel to predict with 95% confidence the maintenance schedule for the ZSE brakes, which should significantly limit downtime.
The disengagement sensor, in turn, confirms whether the smart brake is on or off, a critical piece of safety information for operators addressing problems on the assembly line and maintenance workers servicing equipment.
Beyond their 4.0-compatibility, ZSE brakes have several other advantageous features.
Their braking mechanism, for example, consists of pneumatically released springs. As long as air is being pumped into the brakes, the springs remain open, but once air pressure drops below 5.5 bars, the springs close and brake the load.
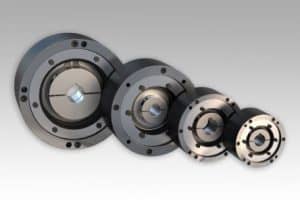
ZSE brakes are available in many bore sizes. These spring-engaged, air-released brakes eliminate the performance problems associated with electrical brakes for consistent, long-lasting performance.
In the case of a power outage, ZSE brakes engage immediately as airflow stops. In contrast, electric brakes take longer to engage in a power outage because electricity requires more time to dissipate from the brakes.
Furthermore, the pneumatically released mechanism does not add heat, which results in cool operation and long life. And because the mechanism requires no energy to operate, ZSE brakes have lower energy costs, as well as higher, more consistent torque capabilities.
Nexen’s ZSE brakes are capable of holding up to 100% of rated torque with zero backlash compared with some other brakes that achieve zero backlash only when operating at as low as 10% of their fully rated torque.
Contributing to the ZSE brakes’ zero backlash are the following features:
- split-hub shaft collar, which produces smooth stopping and precision holding.
- one-piece hub and clamping-collar assembly, which lowers inertia and eliminates spline.
- double-tapered facing, which locks down on the housing and hub to create a solid torque transmission interface.
- one-piece solid hub, which increases torsional rigidity.
Currently available in four standard sizes, the ZSE smart brakes have minimum static torque ranging from 32 Nm for the smallest brake to 300 for the largest. Torsional rigidity ranges from slightly more than 198,000 Nm/rad for the smallest brake to more than 1.34 million for the largest. Brake engagement time ranges from 77 msec for the smallest brake to 162 for the largest.
The bore size of the smallest ZSE brake can be adjusted from 45.875 to 25.4 mm, while the bore size of the largest adjusts from 34.925 up to 74.6125 mm. The smallest brake weighs 3 kg, while the largest weighs 27.6 kg.
The brake life of all four sizes has been tested to 2 million static cycles, with the B10d value is estimated at 4 million static cycles.
In developing the smart versions of ZSE brakes, Nexen created an enclosed housing to keep particulates like sawdust and powders out of the inner workings of the brakes. Not only does the enclosed housing result in smoother operation, but it also reduces the amount of guarding needed to protect machine operators from injury.
The housing is also compact in length and diameter, allowing the brakes to fit onto short shafts and into small spaces.
For more information on 4.0-compatible ZSE brakes, call the Nexen Group at 800-843-7445, or visit www.nexengroup.com.