This article about compressed air preparation written by FESTO, a partner of DirectPneumatics.com.
You need perfect compressed air. You want maximum reliability. We are your compressed air experts.
WE ARE THE ENGINEERS OF PRODUCTIVITY.
Complete concepts for your compressed air preparation
Operators who need high process reliability and availability from their machines have to start right at the beginning – by taking a critical look at their compressed air supply. Particles, water and oil are the natural enemies of prepared compressed air. They have an adverse effect on components and increase energy costs.
The right compressed air quality every time
You can rely on your service unit precisely meeting your requirements or those of your customer’s production operations, regardless of whether these involve standard applications or customised solutions which place extremely stringent demands on purity, pressure and flow rates.
Operational reliability and high performance
Pressure, flow rate and consumption will always be in the green zone: thanks to integrated monitoring functions, you will always be informed about the condition of compressed air filters and can plan needs-orientated maintenance. With their high flow rates yet compact dimensions, our service units allow you to select one size smaller than usual in many cases – for the same performance. Sensors, for example for measuring differential pressure, ensure that the performance density of our service units will remain at the same high level for many years to come.
Air preparation – a worthwhile investment
With correct compressed air preparation, you can significantly increase the service life of your Festo components and systems – and also raise process and product reliability.
Each cubic metre of compressed air contains millions of dirt particles, significant quantitie of water and oil and even heavy metals such as lead, cadmium and mercury. If these are not filtered out, there can be no guarantee that system components will continue to operate trouble-free in the long term.
What is more, these hazardous materials considerably impair product quality. Correct compressed air preparation is therefore vital in order to reduce machine breakdowns and downtime and guarantee process and product reliability.
Excellent reasons why you should pay attention to the quality of your compressed air!
Poorly prepared compressed air causes faults such as:
- Fast seal wear
- Oiled-up valves in system control sections
- Dirty silencers
Possible consequences for users and machines:
- Lower machine availability
- Higher energy costs due to leaks
- Higher maintenance costs
- Reduced service life for systems and components
Compressed air purity in accordance with ISO 8573-1:2010
ISO 8573 is the name for a group of international standards which deal with the purity of compressed air. They define purity requirements for compressed air and specify the maximum levels of solid particles, water and oil that can be present in various classes of compressed air.
Clean solutions
This standard has been mandatory for automation using pneumatics since 2010. It is therefore essential to observe certain parameters in order to achieve energy-efficient compressed air preparation in compliance with this standard.
You should first clarify the following questions:
- What compressed air purity class is necessary for the application?
- What compressed air purity class is necessary for consuming devices such as valves and cylinders?
- What compressed air purity class does the compressor deliver?
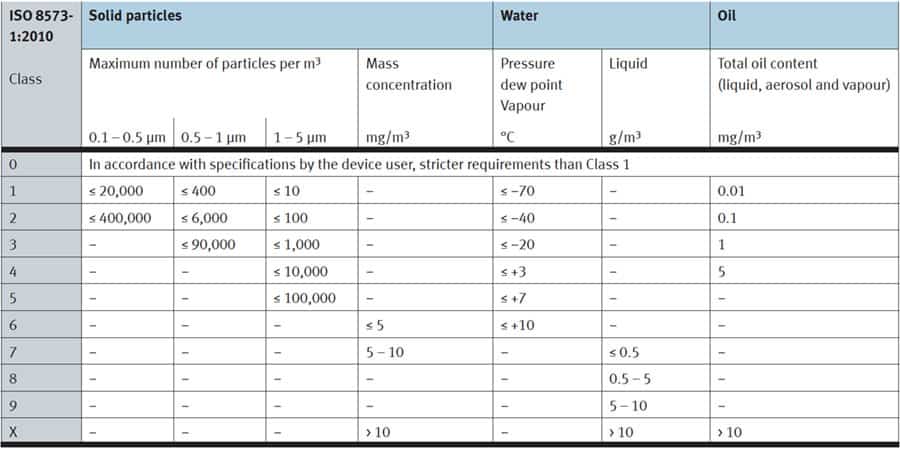
Overview of purity classes in compressed air for particles, water and oil to ISO 8573-1:2010.
Different industry segments and applications require different purity classes
Many industry segments place extremely demanding requirements on compressed air purity. For example, in the food and packaging industries the emphasis is on food safety and full enjoyment of the products, while in painting applications it is important that compressed air should be free of PWIS (paint-wetting impairment substances). Festo service units and filters ensure trouble-free operation.
Here are some examples:
Applications involving direct contact with “wet” food such as beverages, meat, vegetables etc.
Compressed air is used here for transporting or mixing, as well as for general food production. It therefore comes into direct contact with food.
In packaging machines
If compressed air comes into direct contact with food packaging materials, these materials are considered as being part of the food zone.
For both these applications, the following classification applies:
ISO 85731:2010
Particles = Class 1
Water = Class 4
Oil = Class 1
Applications involving direct contact with dry food
Once again, compressed air is used for transporting or mixing, as well as for general food production. It therefore comes into direct contact with food. More stringent requirements apply in these cases, as air humidity is an important factor.
For this specific case, we recommend the following classification of compressed air purity to ISO 85731:2010
Particles = Class 1
Water = Class 2
Oil = Class 1
It is extremely important that these compressed air purity classes should be adhered to in order to ensure the highest possible level of food safety and protect consumer health.
Perfect gloss: PWIS-free painting
When it comes to paint shops, vehicle manufacturers aim to realise zero defects. This means that the compressed air used inpainting applications has to be free of particles and oil. In order to obtain a good bond between the base surface and the paint, this surface must also be clean. Otherwise laborious and costly rework will need to be carried out which will dramatically eat into vehicle manufacturers’ profit margins.
In order to minimise quality problems, the compressed air used must meet the following classes to ISO 85731:2010:
Particles = Class 1
Water = Class 4
Oil = Class 1
Festo components for use in the automotive industry are also produced under PWIS-free conditions.
Clear view: optical displacement encoders for machine tools
Optical displacement encoders, for example for milling machines or other machine tools, require purging air with the following classes to ISO 8573-1:2010 in order to achieve a long service life:
Particles = Class 1
Water = Class 4
Oil = Class 1
This extremely pure compressed air is fed into the machine interior, thus preventing contaminated ambient air from entering the housing. This ensures that oil mist cannot wet and damage the glass scale – a crucial factor for a long service life with displacement encoders.
Meeting purity-class requirements with Festo service units – the series MS
Check to see which products from the series MS would be best for your system.
In the table you will find recommendations from Festo’s experts based on the limit values specified in ISO 8573-1:2010.
Meeting purity-class requirements with Festo service units – the series D
Check to see which products from the series D would be best for your system.
In the table you will find recommendations from the experts at Festo, based on the limit values specified in ISO 8573-1:2010.
The powerful portfolio that meets every requirement: series MS and D
From a simple standard product to application-specific solutions with extremely strict requirements for compressed air quality, Festo’s portfolio makes it easy to find solutions which precisely meet your needs. These are backed by decades of expertise – and a clear understanding of the demands of tomorrow.
Competence meets innovation!
The service units of the series MS and D are the ideal choice for standard tasks. If there are special requirements for compressed air purity, including the high-end area, the series MS with its modular design is the perfect answer.
Our finely tuned product portfolio
Virtually limitless configurations: series MS
Whether the need is for standard components or individual complete solutions, the breadth of the series MS makes it suitable for virtually every application. From highly sensitive applications in the pharmaceutical and food industries to application-specific solutions with heavy-duty flow rates for the automotive industry, the series MS can be used almost anywhere, with both centralised and decentralised installation.
Multiplying advantages: series MS with pre-assembled modules
Pre-assembled modules reduce purchasing costs, increase process reliability and boost your productivity.
They save you up to 50% on time and money.
If you choose a ready-to-install module instead of individual components, you can save yourself a great deal of work, such as the effort involved in selecting 27 items from the catalogue, ordering them, storing them, assembling all 27 parts, integrating them into the system and documenting the whole process. And these are just some of the time- and cost-intensive working steps required.
The advantages of all-inclusive packages with pre-assembled modules
- Engineering expertise of the Festo specialists
- Ability to order a complete system with one ID number
- Reduced logistics costs
- Delivered as a single consignment with a single delivery date
- Fully assembled and tested system
- Guarantee for both components and function
Unique and energy-efficient: the mix of sizes with the series MS
Combines optimum flow rate and compact design
Simply choose one size smaller! An intelligent mix of sizes is one of the hallmarks of the series MS and offers you decisive advantages. It allows the creation of combinations optimised in terms of both space requirements and costs. One example is the combination of MS6 and MS9.
The service unit combination shown in the graphic, designed for an operating pressure of 6 bar, a flow rate of 5,000 Nl/min and a degree of filtration of 0.01 μm, enables you to save up to 30% on component costs and 18% on installation space!
Same performance with lower operating pressure = save costs
An intelligent combination of sizes also offers considerable potential to reduce energy consumption and thus save money. The combination shown, with standard units in size MS6 and fine and micro filters in MS9, significantly reduces the pressure drop within the whole unit compared to that of a unit assembled only using MS6 components. This means that you can reduce the pressure in the main compressed air supply network while maintaining the same flow rate. With this example of a service unit, the supply pressure can be easily reduced from 8 bar to 6 bar. For each bar of pressure reduction, the expected saving on energy costs will be approx. 6% – the higher investment costs will pay for themselves in a very short time. This unique ability to combine sizes thus contributes to the energy-efficient use of compressed air in automation.
Typical application areas for service units with fine and micro filters can be found, for instance, in the painting industry, the food industry, the pharmaceutical and semiconductor industries as well as in measuring and test systems.
Intelligent: series MS with integrated sensors and safety functions
The series MS is setting new standards when it comes to enhanced safety, machine availability and the efficient use of energy. This is thanks to the many functions which you can integrate without any problem.
MS with integrated sensors
Integrated sensors expand the spectrum of possible applications – and make processes more stable. The end result: you become more productive. It is possible to integrate
- Safety functions,
- Energy efficiency,
- Condition monitoring,
- Preventive maintenance and
- Remote monitoring of pressure, flow rates and differential pressure into the series MS without any problem.
The benefits for you:
- Less downtime
- Minimised energy consumption
- Cost control through consumption measurements
- Easy monitoring of process parameters
- Plannable maintenance intervals
- Protection for people and machines
Flow sensor SFAM and MS
This sensor can be integrated into an MS unit without additional installation effort. The two fit together perfectly. Their characteristic features are:
- A highly dynamic starting point of 1%
- Extremely accurate within a huge measuring range of up to 15,000 l/min.
- Absolute flow rate and consumption data
- Easy operation
Pressure and vacuum sensor SDE1 with MS
With the sensor SDE1 for pressure measurement, monitoring and sensing, you have all pressure values constantly under control – for more productivity and faster system commissioning. It is shown here in combination with a compressed air distributor MS6FRM.
Differential pressure sensor SDE1 with MS fine and micro filters
Differential pressure measurement with filter contamination indicator for preventive maintenance to improve compressed air purity and achieve compliance with ISO guidelines. This also helps you avoid excessive pressure drops across filters, which would cost additional energy.
Soft-start/quick exhaust valves MS-SV
MS6-SV-E
For maximum safety for people and machines in the case of a sudden emergency stop in safety-critical areas of a system, MS6-SV-E has a reliable and quick exhaust function. It can also be used for a direct ASInterface Safety at work bus connection with integrated switching status and pressure sensing via the bus.
MS6-SV-D
This is a low-cost alternative to the MS6-SV-E for applications with Performance Levels d to e.
IFA certification
Documented safety – to DIN EN ISO 13849-1, category 4, Performance Levels d and e.
MS6-SV-C and MS9-SV-C
For medium safety requirements up to Performance Level c to DIN EN ISO 13849-1.
Energy efficiency module
MSE6-E2M
The integrated intelligence of this module makes energy saving and condition monitoring easy. The automatic compressed air shutoff and leak detection significantly reduce compressed air losses. A direct fieldbus link allows important process data such as pressure, flow rate and consumption to be uploaded to a controller.
Well-proven: series D in metal or polymer
Series D is available in metal for standard applications and basic functions with decentralised air preparation. It is also available in an inexpensive polymer variant DB which provides core functionality for compressed air preparation. This is ideal for moving machine components, for example where low weight is required.
A classic: the D series
These service units can be found in millions of applications all over the world. They have all of the basic functions that are needed for compressed air preparation in the standard range. There is a choice of four sizes, from micro to maxi, to ensure economic operation. This allows the creation of precise solutions with a broad spectrum of flow ratevalues up to 11,000 Nl/min.
All you have to do is choose and install!
A variety of pre-assembled and pre-tested standard combinations is available to speed up your processes. You have a choice of over 400 variants of pre-assembled service units with various equipment features.
Simple and inexpensive: series DB
The service units of the series DB with their light and extremely strong polymer housings are ideally suited to the core functionalities of compressed air preparation. They offer reliable compressed air preparation in proven Festo quality for applications in non-critical environments. The robust connection technology also guarantees a long service life. Their core functions with pressure regulator, filter regulator and filter regulator/ lubricator combination, are compatible with other components from the metal version. The polymer series is also ideal as a starter model when flow rates of up to 2,000 Nl/min and max. 7 bar are required at the outlet (p2). In typical compressed air networks, service unit combinations of this series achieve a compressed air purity class of 7:4:4.
Safer systems
Another bonus with the pressure regulators of this series is the standard return flow feature via the main valve seat. This rapid return flow also increases system safety further.
Pre-assembled and fully tested: standard combinations
There are four additional, preassembled and fully tested standard combinations available from stock with the new manual on-off valves HE and distributors FRZ. You benefit from shorter delivery times, fast availability and simplified installation – thus speeding up your time to market.
Everything matches: customised solutions
Do you have a specific requirement but cannot find the right product in our catalogue? If so, we can offer you customised solutions, from minor product modifications to completely new developments or ready-to-install solutions.
Take advantage of the comprehensive expertise of our automation specialists and make sure you receive nothing less than an innovative and costeffective solution which reflects the latest technological standards. Comprehensive product testing ensures the best possible quality, while precisely defined interfaces ensure easy integration into your machines.
Ask your Festo sales engineer,who will be happy to help.
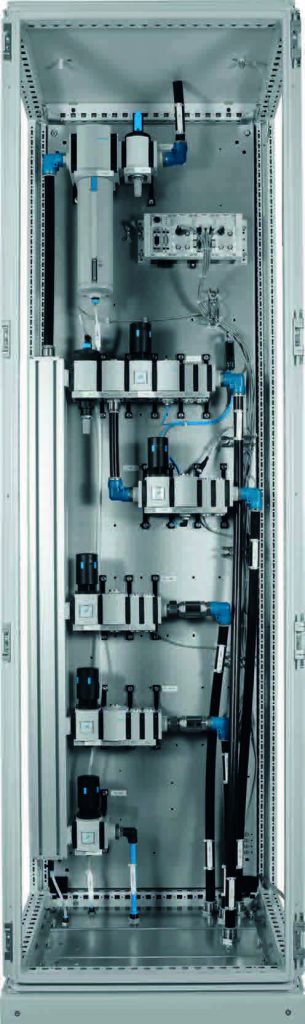
Ready to install: control cabinet for compressed air preparation and distribution, individually tailored for your application
Reach your goals more quickly and easily: engineering tools from Festo
Find the best service unit for your application with our selector tool
It allows you to assemble the right service unit combination for your application. The tool uses typical application parameters to produce a recommendation for the air quality class and components. Alternatively, you can specify a compressed air purity class or assemble a filter cascade directly. If you wish to add any of our most popular service modules, the tool will recommend the right layout and size of the units in accordance with the required flow rate – the service unit is pre-configured.
Overdimensioning thus becomes a thing of the past!
For more details of our selector tool go to www.festo.com/engineering/service_unit
Configure your own individual service unit!
Combinations and individual units can be configured and ordered quickly and easily using the free configurator in our electronic catalogue so that you can be sure you will receive the combination you need.
Make use of our free 2D/3D CAD models in many native formats
Reduce your workload and integrate CAD models for over 25,000 products into your design. These are available in over 45 interchange formats, with many advantages for native formats, such as dynamically generated data.
For more details of our CAD models go to www.festo.com/catalogue
Online Shop and Support Portal for purchasing and after sales
In the Online Shop, it takes just a few clicks to order products, and to receive a delivery date and personal price information. You can also track your orders. This shows you clearly where your order is at all times. Our Support Portal provides you with all product details, including after sales information. It is your central access point for all product information, including information on products which are no longer available. In these cases, the Support Portal will suggest alternative products.
For more details of our Online Shop and Support Portal go to www.festo.com/sp
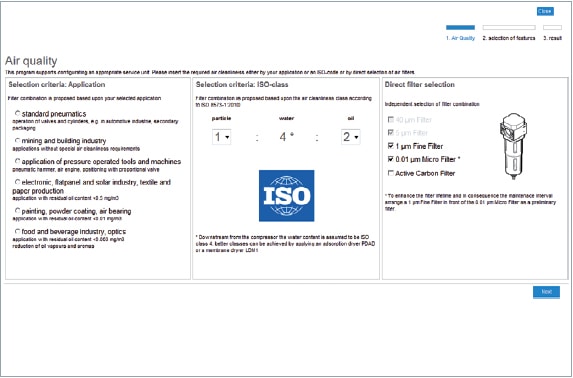
The selector tool allows you to determine the required purity class quickly and accurately.
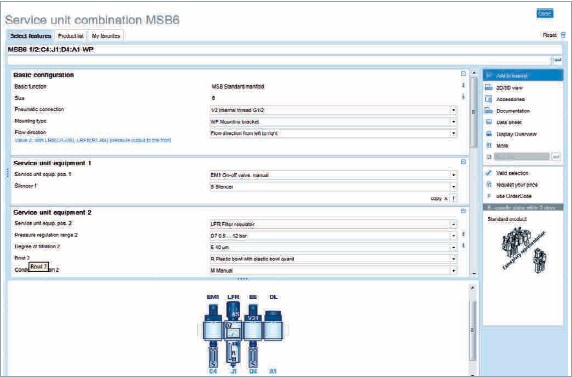
Once the purity class has been determined, the configurator will suggest appropriate products.