The following is from Schmersal, a partner of Direct Pneumatics
What the acceptance of inherently safe Collaborative Robots means for the traditional Industrial Robot
Production demands have and will continue to be a driving force to increase the efficiency on technological advancements. Developing and improving machines and equipment to aid in all phases of the manufacturing process is vital to the success in any industry. One such development was the industrial robot and as with any technology its capabilities are being pushed to reach greater heights. The idea of man working hand in hand with a robot has been a vision for many years. The collaborative robot has now found its place safely on to the factory floor, but where does this leave the traditional industrial robot?
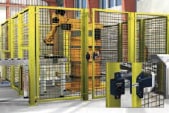
Industrial robot in a robot cage
Take one look at an automated factory floor and you will notice hundreds of moving parts all working in unison to accomplish a task or several different tasks, however not every auto-mated moving part is considered a “robot”. The most recent ANSI/RIA 15.06 robotic standard provides a definition of an industrial robot which includes being automatically controlled having a reprogrammable multipurpose manipulator and programmed in three or more axes; how-ever, as with any standard there may be exceptions or varying interpretations to this definition.
The main purpose of the industrial robot is to perform tasks which are too tedious, strenuous, dangerous or precise for that of a human operator. They have the ability to operate at astonishingly quick speeds and manipulate loads of extremely large dimensions and weights. Although today’s robots may come equipped with safety, they are not inherently safe. Due to the type of dangerous work often reserved for robotic applications and their inability to be failsafe, you will often see the Industrial robot fully enclosed within a room or fenced area; called a robot cell. The entrance to the robot cell will be monitored such that the robot may have a chance to return to a home position before an operator enters and while within the area the robot will essentially be inoperable preventing any physical interaction.
Safety standards have only recently begun to recognize and address the use of collaborative robots as seen with ISO/TS 15066:2016. Why have safety standards been so reluctant to accept a collaborative robot even though there has been decades of successful safe usage of industrial robots? The main reason is safety – since contact between a human and a collaborative robot is not only allowed it is expected. The concept of allowing an operator to be fully exposed to an unguarded automated process was something very few were willing to attempt. However, unlike the industrial robot, a collaborative robot is inherently safe by design, which includes the elimination of sharp edges and pinch points. In addition, the speeds of the robot and payloads which it can handle are limited to typically about 1m/s and 3Kg to avoid harm to the operator if the two were to come into contact. Advancements in technology have allowed for growing acceptance of a robot to be removed from a robotic cell to work side by side with a human.
Although the collaborative robot provides several benefits such as a reduced requirement of hard guarding and now the acceptance of current relative safety standards, there is no reason to believe the traditional robot has outlived its usefulness. Due to the inherently safe measures, collaborative robots are reserved for low speed, simple, repetitive, less accu-rate (when compared to more precise movements capable of an industrial robot) and light material applications. The tooling which the collaborative robot utilizes is also crucial, for example a spot welder, laser or sharp knife may result in serious harm no matter how slow the motion is. The industrial robot will continue to be the choice for fast speeds, complex, accurate, heavy and hazardous material applications.
As with any safety aspect of an application the safety standard for collaborative and industrial robots calls for a risk assessment to identify all foreseeable recognized hazards. Only then can the appropriate type of robot be selected. As discussed in this paper, both offer benefits and both have shortcomings since they are two different types of systems used for different needs and requirements.
Author: Devin Murray
Functional Safety Engineer
TÜV Rheinland ID-No. 4274/11 Machinery
Schmersal USA
Schmersal USA
15 Skyline drive Hawthorne, NY 10532
Tel: 914-347-4775
salesusa@schmersal.com
www.schmersalusa.com